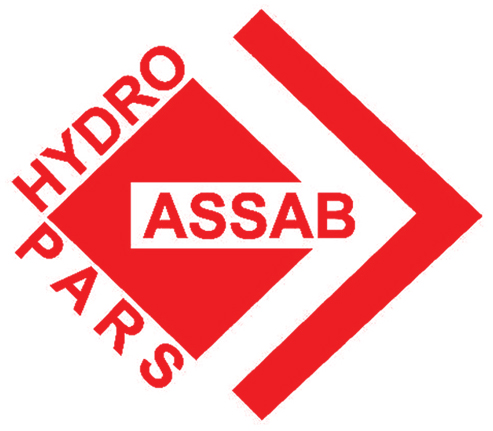
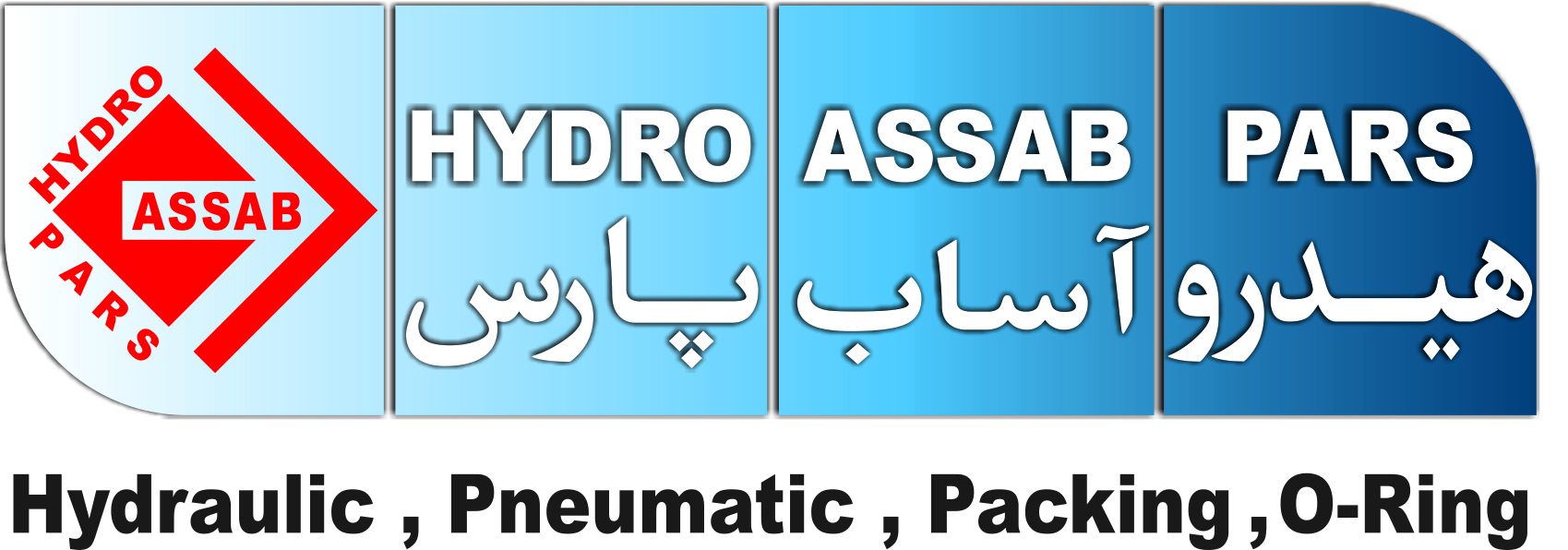
فولاد گسترده ترین آلیاژ صنعتی است و این گستردگی دلیل ندارد جز گستردگی پذیرش عناصر آلیاژی توسط عنصر آهن. از مهم ترین عناصری که به فولادها افزوده می گردند:مس ، سیلیسیم، سدیم، کرم، نیکل، کبالت، کربن، منیزیم، آلومینیوم، مولیبدن، آرسنیک و … می باشند.
قلع
نقطه تسلیم و مقاومت دربرابر کشش فولاد را تغییر نمی دهد ولی در نورد سرد مشکلزا میباشد. زیرا افزایش این عنصر در فولاد باعث ایجاد ترکیباتی میشود که دمای ذوب آنها پایین میباشد.
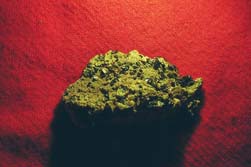
نیکل
چقرمگی و مقاومت به ضربه را به ویژه در دمای پایین و زیرصفر درجه سانتیگراد افزایش می دهد.از درشت دانگی فولاد جلوگیری می کند.استحکام و چقرمگی فاز فریت را می افزاید.مقاومت به خوردگی و مقاومت به حرارت را افزایش می دهد.استحکام تسلیم و استحکام خستگی را می افزاید. سختی و سختی پذیری را می افزاید.رسانایی حرارتی والکتریکی را به مقدار قابل توجهی می کاهد.عنصر مهمی در فولادهای با کاربرد در شرایط سرمایی و فولاد های مخازن نگهداری هیدروژن مایع می باشد.استحکام را در فولادهای کوئنچ نشده یا آنیل شده افزایش می دهد.تماس با این فلز می تواند سبب بروزبیماری هایی همانند حساسیت های پوستی (خارش) و … گردد.
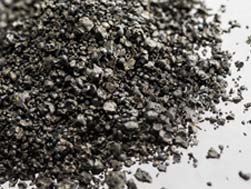
سیلیسیم
استحکام کششی وتسلیم را می افزاید ( به اندازه ی نصف اثر کربن، به ازای هر ۰٫۱درصد سیلیسیم , ۸MPa استحکام تسلیم را افزایش می دهد). تا مقدار ۰٫۳درصد سبب افزایش استحکام شده و تأثیری بر انعطاف پذیری ندارد ولی در مقدار بیش از ۰٫۴درصد انعطاف پذیری را به گونه ی قابل توجهی در فولادهای کربنی کاهش می دهد.
مقاومت به سایش را افزایش می دهد.به طور قابل ملاحظه ای حد الاستیک را می افزاید (کاربرد در فولادهای فنر).نسوزندگی ومقاومت در برابر اکسیداسیون وپوسته دار شدن در دمای بالا را افزایش می دهد.قابلیت ماشینکاری را به دلیل حضورآخال های سیلیکاتی کاهش می دهد.سختی را افزایش داده (کمتراز اثر منگنز) وبه طور میانگین سختی پذیری را می افزاید.قابلیت شکل پذیری و آهنگری راکاهش می دهد.قابلیت جوشکاری را کاهش می دهد.در فولاد های کم کربن، اثر نامطلوب بر کیفیت سطحی دارد.
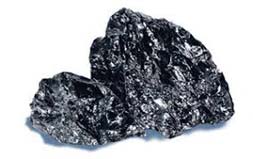
فسفر
مقدار فسفر در فولاد نباید از ۵% تجاوز کند. افزایش بیش ازحد فسفر باعث دانه درشت شدن فولاد می گردد. فسفر خاصیت ماشینکاری، براده برداری، سیالیت مذاب، شکنندگی در حالت سرد و استحکام در حالت گرم را افزایش داده و مقاومت در برابر ضربه را کاهش می دهد.
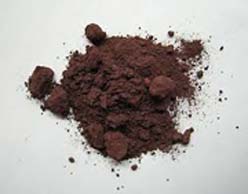
گوگرد
نقطه تسلیم و مقاومت در برابر کشش فولاد را تغییر نمی دهد. گوگرد در ترکیب هر فولادی وجود دارد و به علت کم بودن نقطه جوش ، در مذاب پایداری زیادی ندارد. مشکل اصلی فولادسازان مربوط به پدیده ترک برداری گرم یا سرخ شکنندگی است. لذا سعی می کنند تا حد امکان در صد گوگرد را کمتر کنند . در فولادهای خوش تراش وجود گوگرد عامل مهمی است.در واقع ، یکی از راههای افزایش قابلیت ماشینکاری ،اضافه کردن گوگرد به ترکـــیب فولاد است. وقتی ابزار برش روی سطح قطعه کار می کنند،به علت وجود سولفات منگنز طول پلیسه ها کوتاهتر می شوند و نقش روانکار را نیز ایفا می کنند و در نتیجه صافی سطح بیشتر می شود.
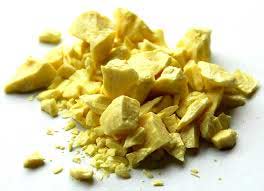
تنگستن
تنگستن کاربرد زیادی در تولید فولادهای ابزار داشته و اخیرا در تولید فولادهای پرآلیاژی مقاوم در برابر حرارت نیز استفاده می شوند. سختی پذیری را افزایش می دهد و کاربیدهای مقاوم در برابر سایش ایجاد کرده و بالاخص از افت سختی در دماهای بالا که امری رایج در نوک ابزار است جلوگیری می کند.
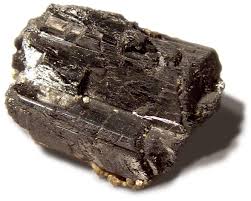
وانادیوم
با افزودن وانادیم به فولادهای ابزار و آلیاژی سختی پذیری آنها افزایش یافته و کاربیدهای کمپلکس در ریزساختار تشکیل می شود.
اخیرا وانادیم به عنوان عنصر آلیاژی در فولادهای کربنی میکروآلیاژی استفاده می شود. وتنها به مقدار کمی کافی است تا افزایش قابل توجهی در استحکام فولاد بدست آید.
این عنصر آلیاژی به دلیل خواص کاربید سازی و کوچک نمودن ریز ساختار به همراه نیوبیم و تیتانیوم در فولادهای میکرو آلیاژی مورد استفاده قرار می گیرد. در فولاد های میکرو آلیاژی عناصر آلیاژی بیشتر از ۲۵% نمی باشد. این عناصر به تنهایی و یا به صورت ترکیبی باعث به وجود آمدن نیترات کربن در ریز ساختار شده و مقاومت فولاد را بالا می برند.
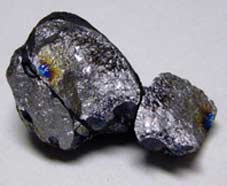
تیتانیوم
همانند وانادیوم دارای خاصیت کوچک نمودن ریز ساختارمی باشد ولی ای خاصیت آن نسبت به وانادیوم بیشتر است. به عنوان یک عنصر میکرو آلیاژی در فولادهای میکرو آلیاژی مورد استفاده قرار می گیرد. در فولاد های ضد زنگ نیز برای از بین بردن اثر مخرب کاربید کروم مورد استفاده قرار می گیرد.
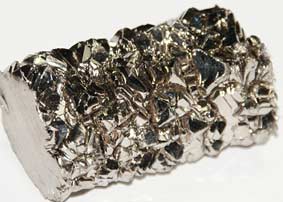
نیوبیم
این عنصر قوی ترین خاصیت کوچک نمودن ریز ساختاردر فولادهای میکرو آلیاژی را دارا می باشد . در فولاد های ضد زنگ اثری مشابه تیتانیوم را داشته و به تنهایی ویا به همراه تیتانیوم مورد استفاده قرار می گیرد.
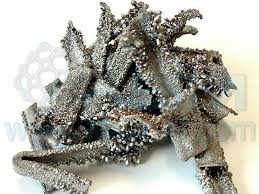
سرب
باعث کم شدن خاصیت نورد در فولاد می شود. کیفیت سطحی فولاد را کم می کند. به دلیل افزایش خاصیت شکل گیری فولاد در فولاد های اتومات بیشتر مورد استفاده می باشد.
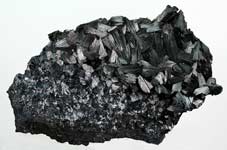
ازت
یک عنصر مخرب می باشد. ازت موجب شکنندگی فولاد شده وخواص خم شدگی آن را تخریب می نماید.
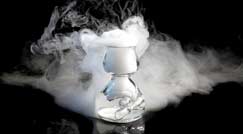
آلمینیوم
این فلز یکی از قویترین عناصر اکسیدزدا و نیز نیترید زدا میباشد، که بدین ترتیب بر حساسیت پیر سازی فولاد تاثیر خیلی مناسبی دارد.
مصرف کم این عنصر به ساختار ریز دانه شدن ساختار کریستالی فولاد کمک میکند. از آنجا که این فلز با نیتروژن، نیترید هایی با سختی بالا ایجاد میکند، یکی از عناصر مهم در فولادهای نیتروره به شمار میرود. آلمینیوم مقاومت سوختگی و پوسته شدن فولاد را افزایش میدهد و به این دلیل یکی از عناصر مهم آلیاژی در فولاد های فرریتی مقاوم به پوسته شدن به شمار میرود.
با آلیژه کردن(آلمینیوم دهی سطحی) میتوان مقاومت فولاد را در برابر پوسته شدن ایجاد کرد.حوزه کریستالی y با افزودن عنصر آلمینیوم شدیدا تنگ تر میشود.
آلمینیوم باعث افزایش شدید نیروی پس ماندزدا میشوم. لذا این فلز یکی از عناصر مهم آلیاژی در آلیاژ های آهنربای دایم که همبسته ای از آهن ، نیکل، کبالت و آلمینیوم است، بشمار میرود.
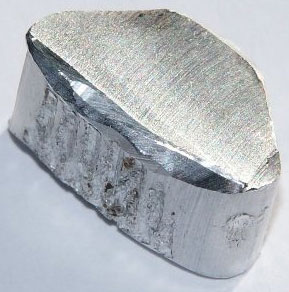
آرسنیک
این عنصر حوزه ی Y را باریکتر و خواص فولاد را خراب میکند زیرا مانند فسفر باعث جدانشینی شدید میشود. نحوه برطرف کردن آن جدانشینی با انجام بازپخت نفوذی به مراتب مشکلتر از فسفر است.این عنصر باعث افزایش تردی برگشت، کاهش شدید میزان چقرمگی و کاهش قابلیت جوشکاری میشود.
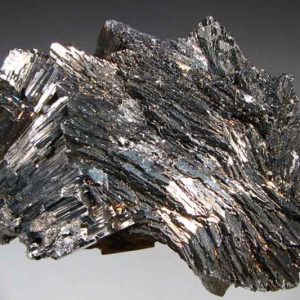
بر
از آنجا که این عنصر در جذب نوترونها نقش مهمی دارد، لذا یکی از عناصر مهم آلیاژی فولادهایی است که در تجهیزات محافظ و کنترل کننده های نیروگاه های هسته ای به کار میرود. با اضافه کردن عنصر بر به فولادهای آستنیتی 18/8 CrNi به واسطه سختی جدانشینی تنش تسلیم و استحکام آنها افزایش یافته ، در صورتی که بطور همزمان مقاومت در برابر خوردگی کاهش می یابد.
جدانشینی ناشی از افزودن عنصر بر باعث بهبودی خواص استحکامی فولادهای آستنیتی مقاوم به دمای بالا میشود.
همچنین این عنصر سختی پذیری عمقی فولاد های ساختمانی را بهبود بخشیده و استحکام مغزی فولاد های کربوره را افزایش می دهد. کاهش قابلیت جوشکاری فولاد در نتیجه حضور این عنصر باید مد نظر باشد.
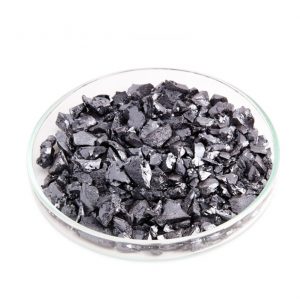
بریلیم
فنر های مارپیچ در ساختمان ساعتها به کار گرفته میشوند، از آلیاژ مس-بریلیم بوده که میتوانند تعداد دفعات ضرب بیشتری را نسبت به فنر های مارپیچ ساخته شده از فولاد فنر تحمل نمایند. آلیاژ های نیکل-بریلیم در برابر خوردگی بسیار مقاوم بوده و در ساخت وسایل جراحی کاربرد فراوان دارند.
این عنصر باریکتر شدن حوزه Y را در پی خواهد داشت. با این فلز میتوان به سختی ناشی از جدانشینی دست یافت که کاهش چقرمگی فولاد را نیز باعث میشود. از خواص دیگر این عنصر اکسیدزدایی و میل ترکیبی زیاد با گوگرد است.
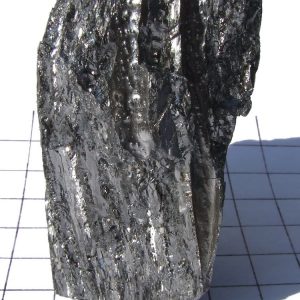
کربن
کربن یکی از مهم ترین و موثر ترین عناصر آلیاژی در فولاد است. هر نوع فولاد غیر آلیاژی در کنار عنصر کربن ، عنصر آلیاژی دیگری مانند سیلیسیم، منگنز، فسفر و گوگرد را نیز در بر خواهد داشت که در زمان تولید فولاد بطور ناخواسته در آن ایجاد میشوند.
افزودن عنصر آلیاژی دیگر برای ایجاد خواص مورد نیاز در فولاد ویا افزایش عمدی منگنز و سیلیسیم، فولاد را به فولاد آلیاژی تبدیل میکند. با افزایش درصد کربن ، میزان استحکام و قابلیت سختی پذیری آن افزایش ، درحالی که ازدیاد طول نسبی فولاد ، قابلیت آهنگری، قابلیت جوشکاری و قابلیت ماشینکاری (با ابزار های براده برداری)کاهش میابد.
عنصر کربن عملا هیچگونه تاثیری بر مقاومت در برابر خوردگی ناشی از آب ، اسید ها و گازهای داغ ندارد.
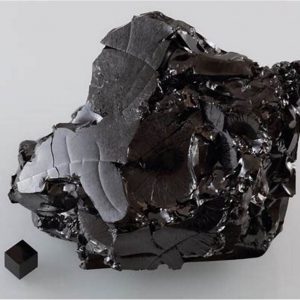
کلسیم
کاربرد این عنصر به همراه سیلیسیم به عنوان یک عضو اکسیدزدا میباشد. کلسیم مقاومت در برابر پوسته شدن المنتهای برقی را افزایش میدهد.
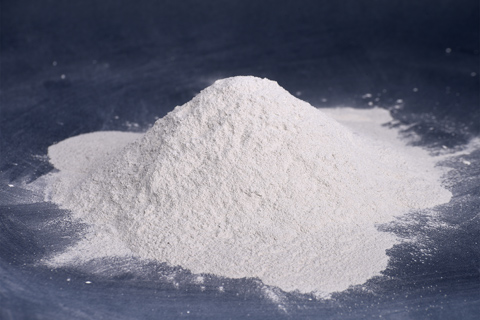
سریم
این عنصر به دلیل خاصیت اکسید زدایی و گوگرد زدایی شدید خاصیت پاک کنندگی داشته و بیشتر همراه با عناصری نظسر لانتانیم، نئودیم، پراسئودیم و دیگر فلزات نجیت نادر به عنوان (میش متال) به کار گرفته میشود.
وجود این عنصر در فولاد های پر آلیاژ باعث افزایش قابلیت شکل پذیری گرم شده و مقاومت در برابر پوسته شدن فولادهای نسوز را بهبود میبخشد.
همبسته ای از آهن با این عنصر به مقدار 70%، سنگ چخماق را می سازند.
به عنوان مواد افزودنی در چدن گرافیت کروی کاربرد دارد.
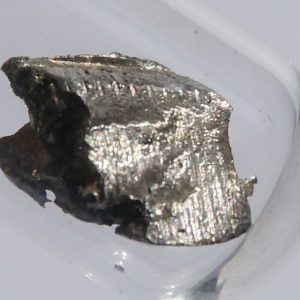
کبالت
این عنصر کاربیدساز نبوده، در دمای بالا رشد دانه کریستالی جلوگیری کرده و مقاومت برگشت و استحکام گرم فولاد را تا حد زیادی بهبود میبخشد، به این دلیل نمیتوان آن را به عنوان یک عنصر آلیاژی در فولاد های تند بر، گرم کار، مقاوم به گرما و دمای بالا به کار گرفت.
وجود کبالت باعث بهبودی تشکیل گرافیت در فولاد میشود، همچنین این فلز باعث افزایش شدید پدیده پس ماند القای مغناطیسی، نیروی پسماندزدا و قابلیت هدایت گرمایی میشود. بدین دلیل این فلز به عنوان عنصر پایه در فولاد های آهنربایی دایم ارزش بالا به شمار میرود.
کبالت تحت بمباران نوترونی تشکیل ایزوتوپ رادیواکتیو میدهد، بدین جهت برای راکتور های اتمی زیاد مناسب نیستند.
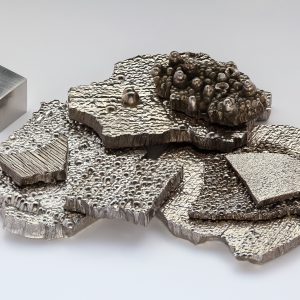
کروم
وجود فلز کروم در فولاد باعث ایجاد قابلیت سختی پذیری آن در روغن یا هوا میشود.
با کاهش سرعت خنک شدن بحرانی به منظور مارتنزیتی کردن ساختار کریستالی آن، وجود فلز کروم باعث افزایش سختی پذیری و درنتیجه بهبود قابلیت بهسازی فولاد میشود. چقرمگی ضربه کمتر و ازدیاد طول نسبی را به نسبت خیلی کم کاهش میدهد. با افزایش درصد کروم در فولاد های کروم دار خالص، قابلیت جوشکاری کاهش میابد. به ازاء هر 1% کروم، استحکام کششی به مقدار N/mm^2 80-100 افزایش میابد.
کروم یکی از عناصر کاربید ساز است. کاربید های کروم باعث افزایش مقاومت برشی و استحکام سایشی فولاد میشود.
استحکام گرمایی و مقاومت در برابر هیدروژن تحت فشار به واسطه فلز کروم بهتر میشود. ضمن اینکه با ازدیاد درصد عنصر کروم، مقاومت پوسته شدن افزایش میابد. ولی برای ایجاد مقاومت خوردگی فولاد ها درصدی از این عنصر به مقدار حد اقل 13% مورد نیاز بوده که باید در ضمینه حل شود.
این عنصر حوزه Y را باریکتر و بلعکس حوزه فرریتی را پهن تر میکند. این عنصر نیز باعث تثبیت آستنیت در فولاد های آستنیتی کروم-منگنز یا کروم-نیکل میشود.
قابلیت هدایت گرمایی و الکتریکی در نتیجه حضور این عنصر کاهش و انبساط گرمایی نیز افت میکند(آلیاژ های ویژه ذوب شیشه).
همزمان با افزایش عنصر کربن مقدار این عنصر تا 3% پدیده هایی چون پسماند مغناطیسی و نیروی پسماندزدا افزایش میابد.
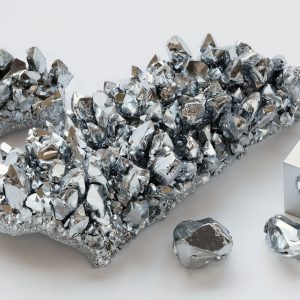
مس
فلز مس فقط در تعداد کمی از فولاد ها به عنوان یک عنصر آلیاژی کاربرد دارد، زیرا این فلز به دلیل تمرکز موضعی در زیر پوسته فولاد و با نفوذ به مرز دانه های سطح فولاد را در مراحل شکل دهی گرم حساس کرده که بدین جهت در بعضی مواقع میتوان این عنصر را زیان آور به شمار آورد.
تنش تسلیم و نسبت تنش تسلیم-استحکام افزایش میابد.
مقدار بیش از 0.3% از این عنصر بر خاصیت پیر سازی عنصر موثر است. قابلیت سختی پذیری بهبود میابد. وجود فلز مس بر قابلیت جوشکاری فولاد بی تاثیر است.
مقاومت در مقابل عوامل جوّی فولاد های غیر آلیاژی و کم آلیاژ، با افزودن عنصر مس به آنها بطور چشمگیری بهبود میابد.
اگر مقدار مس در فولاد های پر آلیاژ مقاوم در برابر اسید بیشتر از 1% بشود، مقاومت آنها را در برابر اسید کلریدریک و اسید سولفوریک بهبود میبخشد.
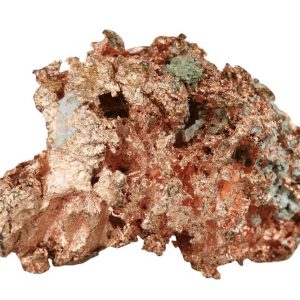
هیدروژن
از آنجا که این عنصر بدون افزایش تنش تسلیمی و استحکام کششی باعث کاهش ازدیاد طول نسبی و کاهش سطح مقطع فولاد شده و آنرا شکننده میکند، یکی از عناصر زیان آور برای فولاد ها بشمار میرود. هیدروژن عامل اصلی و بهبود به وجود آمدن خط زگرگاسیون است. به هنگام اچ کردن هیدروژن بوجود آمده با تشکیل حبابهایی در فولاد نفوذ میکند. هیدروژن مرطوب در دمای بالا باعث کربن زدایی میشود.
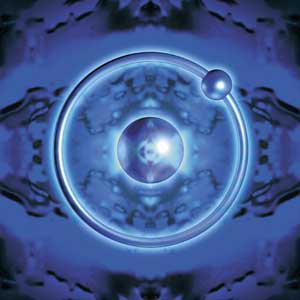
منیزیم
وجود این عنصر باعث میشود که تشکیل گرافیت کروی در چدن بدون اشکال انجام گیرد.
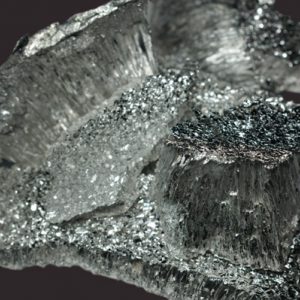
منگنز
منگنز یکی از عناصر اکسیدزدا میباشد. با گوگرد تشکیل سولفید منگنز داده و بدینوسیله اثر مناسب سولفید آهن را خنثی می کند. در فولاد های خوش تراش از عناصر مهم آلیاژی به شمار می رود زیرا خطر شکنندگی داغ را کاهش می دهد.
سرعت خنک شدن بحرانی را بشدت کاهش و به این ترتیب قابلیت سختی پذیری فولاد افزایش می یابد. تنش تسلیم و استحکام فولاد با اضافه کردن منگنز، افزایش یافته، قابلیت آهنگری و قابلیت جوشکاری بهتر شده و عمق سختی پذیری فولاد را به شدت افزایش می دهد.
مقدار بیش از 4% این عنصر با وجود کم بودن سرعت خنک شدن باعث ایجاد زمینه شکنندگی مارتنریتی شده، به نحوی که حوزه آلیاژی به ندرت مورد استفاده قرار می گیرد.
فولاد هایی با مقدار منگنز بیش از 12% با وجود مقدار بالای کربن از نوع آستنیتی است زیرا عنصر منگنز حوزه Y را به شدت پهن میکند. اگر سطح چنین فولاد هایی تحت تنشهای ضربه ای قرار گیرد کار سختی سطح آنها افزایش ولی مغز آنها چقرمه باقی می ماند. بنا بر این چنین فولاد هایی مقاومت سایشی بسیار بالا در مقابل بارهای ضربه ای دارند.
فولاد هایی با مقدار منگنز بیش از 18% درصورت بالا بودن درصد تغیر شکل، قابل آهن ربا شدن نبوده و به عنوان فولاد های ویژه و همچنین به عنوان فولاد های چقرمه سرد در بار گذاری دما پایین کاربرد دارند.
ضریب انبساط گرمایی با افزوده شدن منگنز افزایش ولی قابلیت هدایت گرمایی و الکتریکی کاهش میابد.
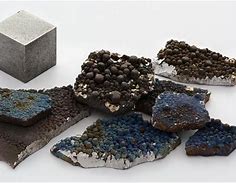
مولیبدن
معمولا این فلز همراه با برخی عناصر آلیاژی دیگر کاربرد دارد. با کاهش سرعت خنک شدن بحرانی توسط این عنصر قابلیت سختی پذیری بهبود میابد. مولیبدن پدیده تردی برگشت یا مرض کروپ را به مقدار زیاد کاهش داده، مثلا در فولاد کروم-نیکل و فولاد های منگنز دار باعث ریزدانه شدن ساختار کریستالی می شود و بر قابلیت جوشکاری در حد مطلوب موثر است. تنش تسلیم و استحکام کشش افزایش میابد. چنانچه درصد مولیبدن از حد معینی زیادتر شود، قابلیت آهنگری فولاد مشکلتر خواهد شد. یکی از عناصر کاربید ساز بوده و خواص برشی فولادهای تندبر را بهتر می کند.
این فلز جزو عناصری به شمار میرود که مقاومت در برابر زنگ زدن را افزایش و به این ترتیب در فولاد های پر آلیاژ-کروم دار و همچنین در فولاد های آستنیتی کروم-نیکل کاربرد دارد. درصد بالای مولیبدن باعث کاهش خوردگی انتخابی میشود، حوزه Y را باریکتر، استحکام گرمایی فولاد را افزایش و مقاومت پوسته شدن را کاهش میدهد.
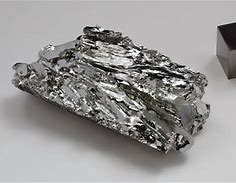
نیتروژن
این عنصر هم میتواند یکی از عناصر زیان آور و هم به عنوان یکی از عناصر آلیاژی فولاد به شمار رود.
زیان آور از این نظر که به واسطه پدیده جدانشینی باعث کاهش چقرمگی و ایجاد حساسیت در مقابل پیر سازی شده، شکنندگی آبی (شکل دهی در محدوده گرمای آبی رنگ 350 تا 300 درجه سلسیوس) در فولاد ایجاد و امکان انحلال بین کریستالی خوردگی-تنش کششی فولاد های غیر آلیاژ و کم آلیاژ را فراهم میکند.
حوزه Y بهتر و ساختار کریستالی فولاد را پایدار میکند. استحکام فولادهای آستنیتی را افزایش و به خصوص باعث افزایش تنش تسلیم و خواص مکانیکی فولاد در گرما می شود. یکی از عناصر نیتریدساز بوده و بدینوسیله سختی سطحی فولاد هارا در مرحله نیتروره کردن افزایش میدهد.
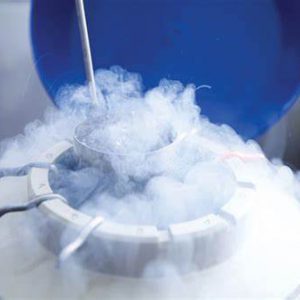
نیوبیم/کلمبیم
تانتالیم
این عناصر معمولا همراه با یکدیگر گرفته شده و به سختی از یکدیگر قابل تفکیک می باشند. از عناصر کاربیدساز بوده و به این ترتیب از عناصر پایدار کننده مهم در فولاد های مقاوم به مواد شیمیایی به شمار می روند. هر دو عنصر فرریت ساز بوده و حوزه Y را تنگتر میکند. به دلیل افزایش استحکام گرمایی و استحکام خزش به وسیله نیوبیم، معمولا به عنوان عناصر آلیاژی فولاد های آستنیتی مقاوم به دمای بالا در ساخت دیگ بخار، کاربرد دارند. تانتالیم از سطح جذبی گسترده ای برای نوترونها برخوردار بوده و بدین سبب فولادهای نیوبیم با مقدار کم تانتالیم در ساختمان نیروگاه های اتمی به کار گرفته می شوند.
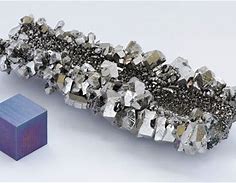
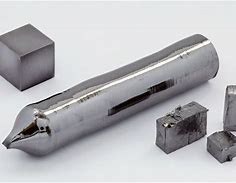
اکسیژن
یکی از عناصر زیان آور فولاد است، به دلیل تاثیرات ویژه نوع و میزان ترکیب آن در فولاد و همچنین شکل و کیفیت توزیع آنها مهم است. بعضی از خواص مکانیکی از جمله چقرمگی ضربه به ویژه در جهت عرضی کاهش ولی تمایلاتی چون شکنندگی ناشی از پیر سازی فولاد، شکنندگی داغ، شکست در جهت الیاف و شکست مورّب تشدید میشود.
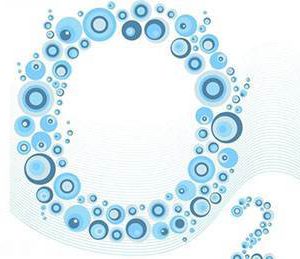
آنتیموان
به دلیل کاهش خواص چقرمگی فولاد، این فلز جزو یکی از عناصر زیان آور در فولاد میباشد، این عنصر حوزه کریستالی Y را نیز باریکتر میکند.
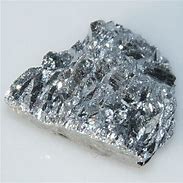
سلنیم
از آنجایی که قابلیت بهبود مراحل ماشینکاری فولاد های خوش تراش توسط این عنصر نسبت به گوگرد بالاتر است، کاربرد آن همانند گوگرد در این فولاد ها است. این عنصر مقاومت در برابر خوردگی فولادها را کاهش ولی نسبت به نوع مشابه گوگردی کمتر است.
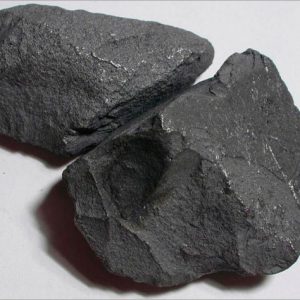
زیرکونیم
این فلز یکی از عناصر کاربیدساز است، به عنوان یک ماده کاربردی متالوژی در فولاد اکسیدزدا، نیتریدزدا و جاذب گوگرد می باشد، زیرا محصول اکسیدزدا شده ی خیلی کمی از خود باقی می گذارد. افزوده زیرکونیم به فولاد های خوش تراش کاملا آرام شده تاثیر بسزایی در تشکیل سولفید مربوطه و در نتیجه جلوگیری از شکنندگی داغ فولاد دارد.
عمر المنتهای برقی را افزایش داده و حوزه کریستالی Y را تنگتر می سازد.
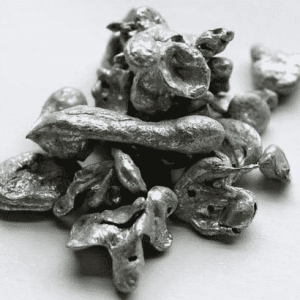
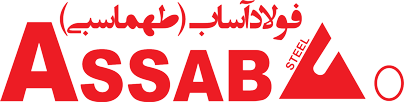